Measurements and Diagnostics
We offer comprehensive measurement services for electrical (LV and MV) and teletechnical equipment, networks and installations. We support clients at the stage of acceptance measurements, periodic measurements and post-failure diagnostics.
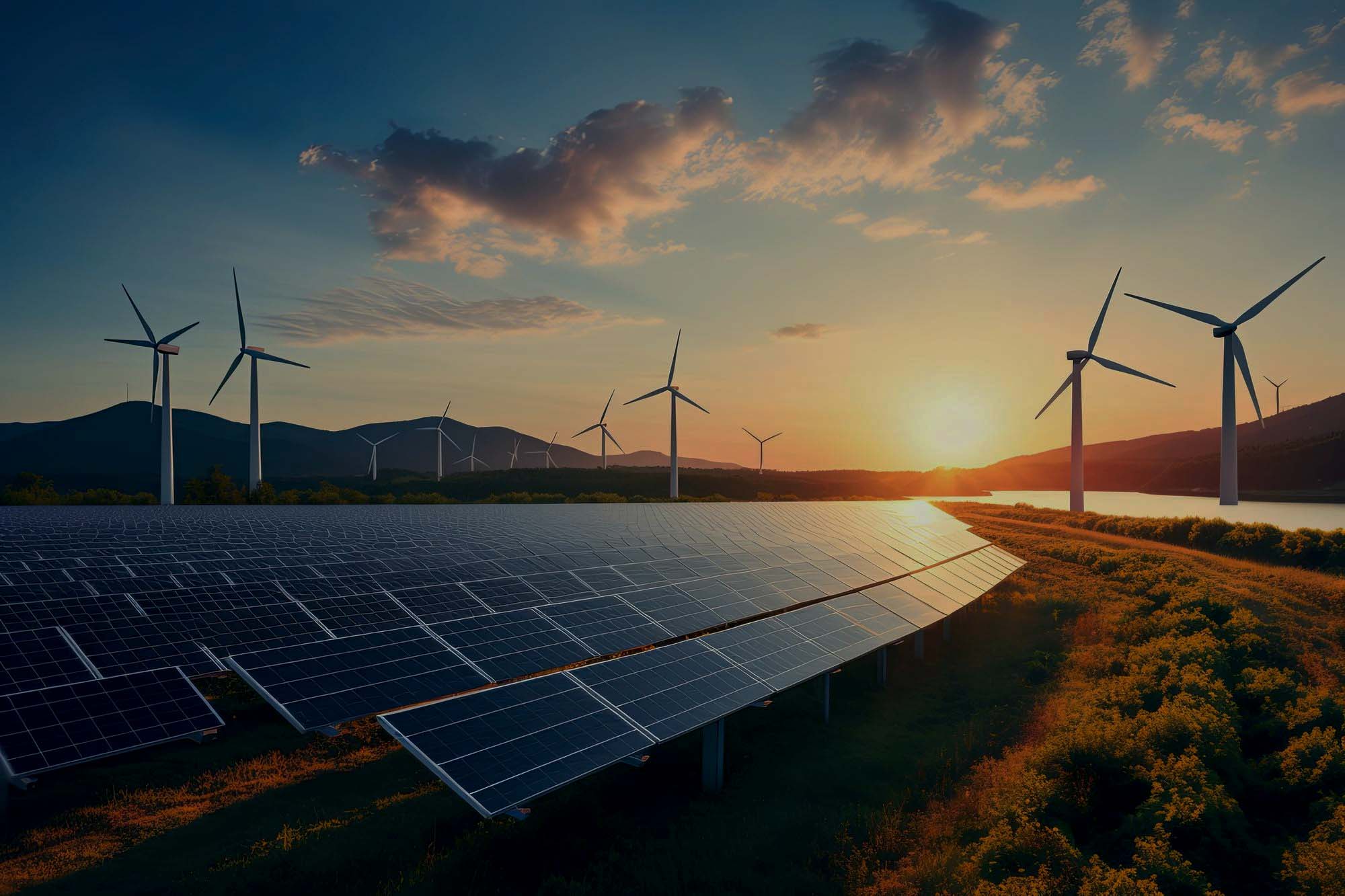
Learn the details of our services
PGMEX offers comprehensive acceptance, periodic inspections, and post-failure diagnostics of transformer stations. Activities include technical checks and maintenance of switching apparatus, testing transformers, and a complete range of measurements for equipment and automation systems.
PGMEX offers a wide range of measurement services for devices, networks, and electrical installations. Measurements are conducted using specialized instruments with necessary calibration and certification.
Our offer includes:
- Insulation resistance measurements
- Line/loop impedance measurements
- Three-phase current measurements
- Ground resistance measurements
- Soil resistivity measurements
- Small resistance measurements
- Simultaneous contact opening/closing measurements
- Breaker operating times measurements
- Continuity measurements of protective and equipotential bonding
- Step and touch voltage measurements
- Testing of current and voltage transformers
- Overcurrent protection testing
- Voltage tests of cables and MV switchgear
- Irradiance measurements
- Solar irradiation measurements
To ensure correct and safe operation of power supply systems and power extraction systems, regular transformer inspections supplemented by maintenance activities are required. Recommended inspection intervals and scope should be specified in the operating instructions based on the manufacturer’s guidelines. In industrial facilities (including energy operations), the typical inspection period is one year, conducted during economically justified shutdown periods.
Voltage tests of cables and MV equipment are fundamental control measurements for commissioning the facility after construction, repair, or fault removal. During tests, manufacturing defects (quality of production), installation and transport defects (mechanical damage, connection damage), and operational defects (degree of cable and joint insulation wear, moisture content) are detected.
Power System Protection Automation systems (EAZ) monitor and detect disturbances in the normal operation of the network and selectively disconnect sections in a fault state or showing irregularities.
PGMEX provides integration, configuration, diagnostics, and service for EAZ systems.
Power quality measurements involve a comprehensive analysis of electrical parameters such as voltage stability, frequency, harmonic distortions, voltage asymmetry, voltage fluctuations, and power factor. Their purpose is to assess compliance with industry standards and identify risks associated with improper interaction of generating units with the power grid. Power quality measurements verify qualitative analyses and may be required by the RSO in the compliance assessment process with Operating Instructions. Proper execution enables the proposal of appropriate solutions, such as active/passive filters, static reactive power generators, reactive power compensation systems, and voltage stabilizers.
Power quality measurements involve a comprehensive analysis of electrical parameters such as voltage stability, frequency, harmonic distortions, voltage asymmetry, voltage fluctuations, and power factor. The purpose of these measurements is to assess compliance with industry standards and norms and to identify risks associated with improper interaction of generating units with the power grid. Power quality measurements verify qualitative analyses and may be required by the Relevant System Operator during the compliance assessment process with Operating Instructions. Proper execution of these measurements enables the proposal of appropriate solutions, such as active/passive filters, static reactive power generators, reactive power compensation systems, and voltage stabilizers.
Thermal Imaging Cameras – Inspections of Photovoltaic Panels: Drones equipped with special thermal imaging cameras are capable of detecting infrared radiation emitted by photovoltaic panels. This allows for the observation of the temperature of individual cells and areas of the panels.
Thermal Detection of Anomalies: Using a thermal imaging camera, potential anomalies in panels such as damage, current leaks, poor connections, or overheating areas can be detected. These issues can affect performance, user safety, and the longevity of the panels.
Thermal Imaging for Speed and Efficiency: Drones enable thermal imaging inspections of photovoltaic panels over large areas in a short time. This allows for the quick identification of potential issues in PV installations. The bird’s-eye view provided by drones allows the camera to reach places that are typically inaccessible.
Preventing Failures with Thermal Inspections: Regular thermal inspections can detect problems in panels before they escalate, leading to failures or reduced system performance.
Time and Cost Savings with Drone Thermal Imaging: Traditional methods of inspecting photovoltaic panels require time-consuming manual examinations on site. Drone-based thermal imaging is more efficient, saving time and reducing costs.
Thermal Documentation and Data Analysis: Thermal data collected during drone flights can be recorded as thermograms and video footage, which can then be analyzed. Drone thermal imaging allows for monitoring changes over time and creating detailed reports.